This is a short video of a blacksmith making a set of tongs. I didn't make tongs but this will give you a good idea of the forging process. It shows how easy it is to deform the metal when it is hot, his hammer strikes are smooth and accurate so he is shaping the metal, I pretty much deformed it.
Sunday, April 29, 2012
Saturday, April 28, 2012
Blacksmith Course Pt.2
Things I learned in the two days at blacksmith school:
1. strike while the iron is hot has real meaning in a forge. From the time that the piece comes out of the fire until it has cooled to were hitting it is a waste of time is a very short time, hence, strike while the iron is hot.
2. you have a short window of opportunity while the steel is hot, so you have to know what you are trying to achieve. As a beginner I really had little clue of what to do, even though I had some idea of what I hoped would result from my efforts. Often I spend the next time I heated the steel fixing mistakes from the last time. Daniel figures I took 5 to 10 times longer to complete my pieces than he would.
3. I am not as good a hammerer as I thought. Upon thinking about it I haven't swung a serious hammer, for any length of time in years. I don't drive long spike, I drive long screws, so, when it came time to hammer steel I was inaccurate and did not hit the hot steel hard enough to accomplish much of anything some times.
4. when steel gets to 1440 degrees Fahrenheit it is no longer magnetic, very cool. Daniel showed me that the steel piece would attract a magnet along it length until it got to the real hot section and then it would not hold. When the section cooled, the magnet held. (very cool)
5. steel can burn, not just discolour and look burned, but burn. I had a small piece in the fire for too long and then suddenly, the piece was smaller and the tip was gone and the rest of the tip looked like charcoal more than steel.
6.The more practical things I learned is that I really admire what Daniel can do with steel in his forge, but I have no intention or desire to begin learning how to do those things myself. If there is a tool that I really want and can't find I'll have Daniel make it rather than try and make it myself. I have learned that it takes;
annealing the steel,
forging and shaping
cooling,
hardening
and tempering to make steel (like files and leaf springs) into useful tools.
Those are the steps, each step takes tools, many of which were new to me and skills, all of which were new to me.
While at Forged Link I made two lathe chisels, a large roughing gouge and a very large straight scraping chisel. You can see the blanks sitting on the anvil. The top piece was heated and shaped into the gouge on a swage block after first having the tang drawn out from the original rectangular piece of leaf spring. Drawing the tang was a hammer and tongs sort of experience and one that showed me just how poor a hammerer I really am. ( shaped photo to follow in part 3)
The lower piece was cut to its basic shape with a grinder and cutting wheels. Then all that was necessary was rounding some corners and shaping the rough bevel on the edge. That was straight forward enough that it didn't take even me very long.
After the pieces were formed, cooled and tempered there is still final shaping and sharpening, two tasks to be completed in my home workshop. Tasks that will be attended to shortly and then handles will have to be made before the chisels can be used on my lathe.
The chisels are bigger than any I have seen for sale and probably more cost effective, and....I made them. (with help) and making my own tools has proven to be an educational and rewarding experience.
1. strike while the iron is hot has real meaning in a forge. From the time that the piece comes out of the fire until it has cooled to were hitting it is a waste of time is a very short time, hence, strike while the iron is hot.
2. you have a short window of opportunity while the steel is hot, so you have to know what you are trying to achieve. As a beginner I really had little clue of what to do, even though I had some idea of what I hoped would result from my efforts. Often I spend the next time I heated the steel fixing mistakes from the last time. Daniel figures I took 5 to 10 times longer to complete my pieces than he would.
3. I am not as good a hammerer as I thought. Upon thinking about it I haven't swung a serious hammer, for any length of time in years. I don't drive long spike, I drive long screws, so, when it came time to hammer steel I was inaccurate and did not hit the hot steel hard enough to accomplish much of anything some times.
4. when steel gets to 1440 degrees Fahrenheit it is no longer magnetic, very cool. Daniel showed me that the steel piece would attract a magnet along it length until it got to the real hot section and then it would not hold. When the section cooled, the magnet held. (very cool)
5. steel can burn, not just discolour and look burned, but burn. I had a small piece in the fire for too long and then suddenly, the piece was smaller and the tip was gone and the rest of the tip looked like charcoal more than steel.
6.The more practical things I learned is that I really admire what Daniel can do with steel in his forge, but I have no intention or desire to begin learning how to do those things myself. If there is a tool that I really want and can't find I'll have Daniel make it rather than try and make it myself. I have learned that it takes;
annealing the steel,
forging and shaping
cooling,
hardening
and tempering to make steel (like files and leaf springs) into useful tools.
Those are the steps, each step takes tools, many of which were new to me and skills, all of which were new to me.
chisel blanks |
The lower piece was cut to its basic shape with a grinder and cutting wheels. Then all that was necessary was rounding some corners and shaping the rough bevel on the edge. That was straight forward enough that it didn't take even me very long.
After the pieces were formed, cooled and tempered there is still final shaping and sharpening, two tasks to be completed in my home workshop. Tasks that will be attended to shortly and then handles will have to be made before the chisels can be used on my lathe.
The chisels are bigger than any I have seen for sale and probably more cost effective, and....I made them. (with help) and making my own tools has proven to be an educational and rewarding experience.
Thursday, April 26, 2012
Blacksmith Classes Pt. One
I just got in from Hanover and boy are my arms tired, bah dump bump. The last two days have been spent in the immediate vicinity of one of these.

And close to these:
I spend two very interesting, educational and somewhat humbling days with Daniel at Forged Link Blacksmith's Forge in Hanover ON. My arms are not tired because I flew home, they are tired because for several hours a day I was pounding hot steel with a big hammer while holding the piece in long steel tongs with the other. (while trying to sort out at least 6 things at once and not get burned).
More details of the experience and the results of my efforts and Daniels skill and patience to come.
Before I continue with my saga I think you should look at forgedlink.blogspot.com, and back at your collection of recent Lee Valley Catalogues. Dan's knives where on a very recent supplementary catalogue cover.

And close to these:
Not all the hammers, just the ones that are used regularly. Even I used four different ones during the two day. |
And using some of these:
there are tongs for all occasions and applications, a black smith generally makes his own. |
More details of the experience and the results of my efforts and Daniels skill and patience to come.
Before I continue with my saga I think you should look at forgedlink.blogspot.com, and back at your collection of recent Lee Valley Catalogues. Dan's knives where on a very recent supplementary catalogue cover.
Monday, April 23, 2012
Today is a full day in the work shop. What am I doing? It seems like a dozen small jobs, probably it will be more than a dozen. Right now it is lunch time and I'm eating and working on the blog while glue and finishes dry.
First thing I did was finish two window frames like the one in the photo. The frame as you can see is just large enough to be a pain. The short sides are 55 inches and the long side is 77 inches. The 1 x 2 is long enough that the 45 degree angles were easier to cut with my hand saw that to fiddle around with the mitre saw, though I did use the Mitre saw to cut up the 1/4 inch plywood used for the corner plates. This wasn't a tough job, just awkward, and as always, the second one was much easier to make than the first.
After I finished gluing and screwing these frames I glued up two cutting board blanks. I can glue four or five at a time depending on the size and design of the cutting boards but at this time I have a bit of a rush on for one of the boards and only had material ready for one other board. The boards sit for 24 hours before I pop them out of the clamps and begin planning, and sanding. I use Titebond III for my boards, once that glue is set I am pretty sure the glue is stronger than the wood. This set of cutting boards will be oak, roasted birch and maple, they look good and should last for years and years.
While that is drying I stained three, three board book shelves, three different colours, of course. That means three brushes and three sets of rags to wash, so it isn't really one task, it is three. To top off the dry time I sprayed a couple of dino puzzles with my favourite spray lacquer.
I really couldn't say whether this is the best spray lacquer on the market, what I do know is that it is the one with which I am most familiar.
Just about done at the desk and it is now time to return to the basement workshop and paint the window frames white, it will take a couple of coats and see if the stains are dry enough (I use water based stain) for me to spray.
Tomorrow I am off to a blacksmith workshop for a couple of days. I think it will be very exciting.
Friday, April 20, 2012
Tool Box Saw
![]() |
cut down hand saw, about 19inches in length. |
I like to drop into the Re-Store when I am in the neighbourhood or when we are working on a project that needs good materials that don't really have to match. The light fixtures in my work shop are a classic example of something from the Re-Store as well as the beige paint that I splashed around the garage when we bought this house. I think the Re-Store is a good organization and I have always got what I paid for from them.
Anyway, I saw this funny little saw while I was shopping and for $3.00 I figured even if it was useless one of my crafty friends could paint a picture on it and I could hang it on the work shop wall. The other day I was cleaning up in the shop and found the saw where it had been stashed. It is not useless, and will not have a picture of chickens or cows painted on it, it is a very good little cross cut saw. It appears that it was a full sized saw that was broken off or cut down to fit in a tool box and maybe even had its own mitre box. Now on my list of to-does is to polish the little saw up and give it a spot in my working collection of hand saws. It will fill the roll of a tenon saw very nicely.

It is an extra kick when I get something like the $3.00 saw, that gives added value for my money or effort. The possibility of finding something like that is what takes me into flea markets and places like the Re-Store.
Wednesday, April 18, 2012
You've Got to See This, Wood Workers
Table Saw safety is much in the wood working news right now. We have all had some sort of incident at our table saw. It is not that table saws are generally more dangerous than other tools, I don't think. My feeling is that we have spent so much time working on our table saws that we have begun to treat them with casual contempt. In my shop the table saw came first and the router table came last, and I am ultra careful around the router table, and...the saw has nicked me twice, both times, my fault.
Tom at: New Wood Worker. com has a very important video for all of us to see.
Thank you very much Tom. Yes, I think you are a little bit crazy, but in a good for the rest of the woodworking world way.
Tom at: New Wood Worker. com has a very important video for all of us to see.
Thank you very much Tom. Yes, I think you are a little bit crazy, but in a good for the rest of the woodworking world way.

Monday, April 16, 2012
Why Wood Work?


Trees are peaceful, working with wood helps bring peace too.
Friday, April 13, 2012
Barn Board Bird House
K's bird house, in Clara's tree |
My initial thought had been to plane them down and have nice clear pine boards for projects but after some more thought I decided to use them on things that would benefit from their weathered appearance. Nothing came to mind until I was looking for something that my 2 1/2 year old grandson could build in the shop with Opa. Kieran has already helped put his sisters crib together as well as assemble the book cases in his family room, he even has his own tool belt. He is actually a help, I hold the drill driver and he pushes the trigger and we drive the screws together.
Building the bird house was an interesting project, I looked up the specifications matching houses to species of birds on the computer. As well as giving proper hole sizes ( smaller than I would have thought) it recommended that there not be a perch in front of the hole. without the perch predator birds have nothing to stand on while pushing their heads into the house to attack chicks or break eggs.
This project also had a different method of work, I chose to do all the cutting of the barn board with hand tools. I have experience with reclaimed lumber and know that there can everything from blown sand to buck shot in those old boards. I though if I cross cut and ripped the boards with hand tools I would have a better feel for possible trouble, and....it is a worth while skill to keep up.
Driving in the screws, I hold the drill, he pushes the button |
I cut the boards to size on afternoon during Kieran's nap and pre-drilled all the holes for assembly. The next day we put it together.
K spreading glue on the bottom |
Hammering the bottom in |
I won't be too long and Clara will get her chance in the workshop too.
Wednesday, April 11, 2012
Table Saw Sled
I haven't really been up to much of interest in my shop over the last couple of weeks. Next month I am going to be selling cutting boards at a local show and so that is mostly where my attention has been going. Cutting boards are nice pieces of wood, but not really very interesting to show off on a blog.
So, what I have been doing is cruising around the net looking for things to share with you folks out there. There is so much stuff on the net I feel confident that not everyone has seen everything I am sharing.
Today I have a You tube video of a very interesting table saw sled made by Bridge City Tools Works. Bridge City is very nearly as high as you can get when you go High End. Their tools are always reviewed favourably and sadly too rich for my blood.
Anyway, take a look at this Parallelogram Table Saw Fence. I do think it is cool. I especially like the idea of cutting the dovetails on the table saw.
So, what I have been doing is cruising around the net looking for things to share with you folks out there. There is so much stuff on the net I feel confident that not everyone has seen everything I am sharing.
Today I have a You tube video of a very interesting table saw sled made by Bridge City Tools Works. Bridge City is very nearly as high as you can get when you go High End. Their tools are always reviewed favourably and sadly too rich for my blood.
Anyway, take a look at this Parallelogram Table Saw Fence. I do think it is cool. I especially like the idea of cutting the dovetails on the table saw.
Tuesday, April 10, 2012
Cordless Impact Drivers

The impact driver is one tool that I have yet to acquire since, so far I haven't needed one. The deck at the back of the house was built by a pro that we hired in for the job; the framing in the basement was done by a contractor, mostly, and so I have not needed the power that an impact driver brings to the game.
As an additional point to Andy's write up, a hammer drill moves the drill bit in and out to create the hammer effect. An impact driver creates rotational hammering and so those two tools do two different jobs and are not really interchangeable. The few times that I have had to drive long deck screws I have been prepared to stretch my 14.4 volt drills to their limit. But, make no mistake, tools are not designed to work to their maximum over and over again. When I used to sell tools I always tried to get the customer to recognise how much they were expecting of the tool and then encouraged them to buy a tool that was robust enough for the task. ( cheapest is not the best value if your time is worth anything)
Saturday, April 7, 2012
Kreg Rip Cut
http://www.thetoolstore.ca/view.asp?Kreg-KMA2675-Rip-Cut-Circular-Saw-Guide_13754

Check out the video on thetoolstore.ca page. This is a tool that has a place in most peoples shops. I have an early version of this tool made by another company and Kreg has made some useful improvements to their model, well done.

Check out the video on thetoolstore.ca page. This is a tool that has a place in most peoples shops. I have an early version of this tool made by another company and Kreg has made some useful improvements to their model, well done.
Wednesday, April 4, 2012
Good Ideas are Often Simple Ideas
I was surfing around the net and saw this:
Get-a-grip-and-save-your-back
I am going to be bold enough to claim I had though of doing this many times in the past, and honest enough to admit that I hadn't gotten around to it.
I like super cool new tools and whiz bang ideas, but I love simple, cheap and effective solutions even more.
Hooray for Popular Woodworking.
Get-a-grip-and-save-your-back
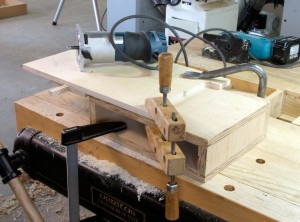
I am going to be bold enough to claim I had though of doing this many times in the past, and honest enough to admit that I hadn't gotten around to it.
I like super cool new tools and whiz bang ideas, but I love simple, cheap and effective solutions even more.
Hooray for Popular Woodworking.
Monday, April 2, 2012
Apartment Tool Kit part 3

A while ago we added the 1/2 variable speed corded hammer drill to our apartment tool kit. That drill can be very useful, with the correct attachments you can use that drill to sand, polish or mix paint, all jobs that come up and can be done without a work shop.
The next tool I think a person needs is a jig saw. Many people buy a circular saw but they are an aggressive tool and also single purpose. A jig saw is much easier for a beginner to control and more versatile. A jig saw will cut a pretty straight line, almost as straight as a circular saw in unskilled hands but also the jig saw will cut curves and inside curves, things that the circular saw can't do. Sometimes an apartment or 1st time home owner needs to cut plastic or copper plumbing pipe too, with the correct blade the jig saw does that job well too.
Jig saws, like all tools come in a variety of price ranges. When you go to buy your saw ask to hear and hold it plugged in and running. As the saws improve in quality they usually get quieter and run more smoothly, the smoother the saw runs, the easier it will be to control while you are making your cuts. Also if the saw is very noisy your neighbours on the next balcony or next yard may start to complain.
A site reviewing and rating Jig Saws
Subscribe to:
Posts (Atom)